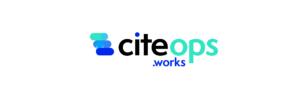
CiteOps streamlines short-term planning, resource allocation, and shift execution by providing real-time visibility, enabling teams to coordinate tasks, optimize resources, and improve operational efficiency across shifts and departments.
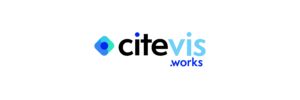
CiteVis provides real-time insights into operational performance. It helps mining and metals teams monitor progress, identify bottlenecks, and make data-driven decisions by transforming complex operational data into clear, actionable visual reports.
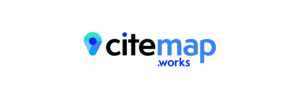
Interactive digital map with real-time visibility of plans, people, equipment, hazards and work shown in space and time.
Our Story
We started out as consultants many years ago, making spreadsheets and whiteboards for mine sites. We realised these tools were not really doing the job: they weren’t sustainable and were hard for people to use.
Since launching our first product Fewzion over a decade ago, Commit Works’ suite of software has helped operations eliminate day-to-day variability, empowered committed and coordinated teams, and helped teams to sustainably improve results.
For 10 years we have led the digital transformation of integrated frontline work management. Our software is quicker to install, easier to learn and use and returns larger benefits in shorter timeframes than any other solution on the market.
We now work with customers on five continents, across multiple resource types and mining methods.
Our Customers
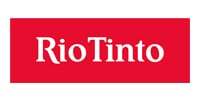
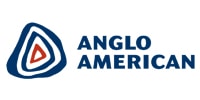
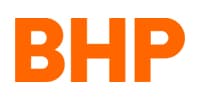
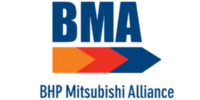
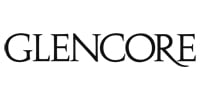
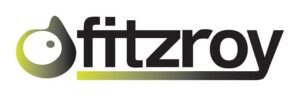
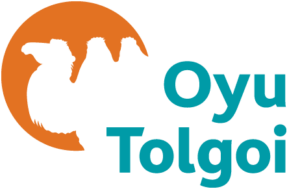
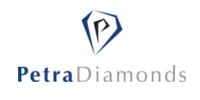
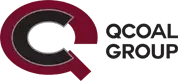
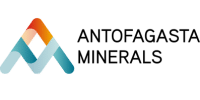
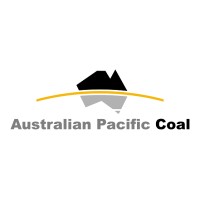
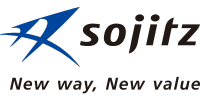